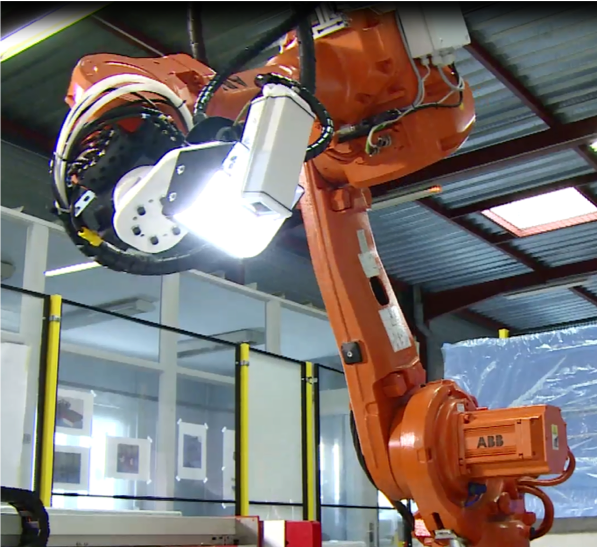
In recent years there has been a substantial increase in the use of composite structures for various applications and for new generation airplanes. The various forms of composite materials offer advantages of light weight, design flexibility, high specific stiffness and specific strength.
For example the use of composites in the aviation industry spans from components to large structures, some examples are helicopter rotor blades and radomes, engine nacelles, cowling and aircraft fairings, empennage (rudder, elevator…), fuselage and wing structure.
There are numerous methods for fabricating composite parts. Many of them were developed to meet specific design or manufacturing challenges. Therefore, the selection of the right method for a particular part will depend on the materials, the part design and end-use or application.
To meet the needs of Industry 4.0, the partners of Composite Alliance Group (CAG) have developed automation tools and control solutions.
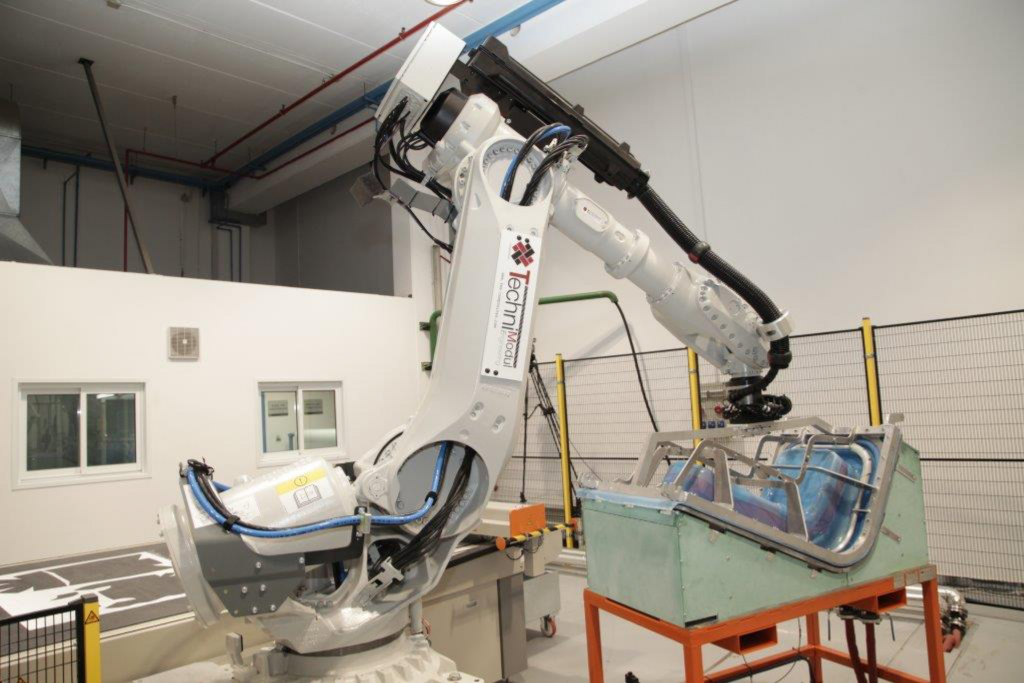
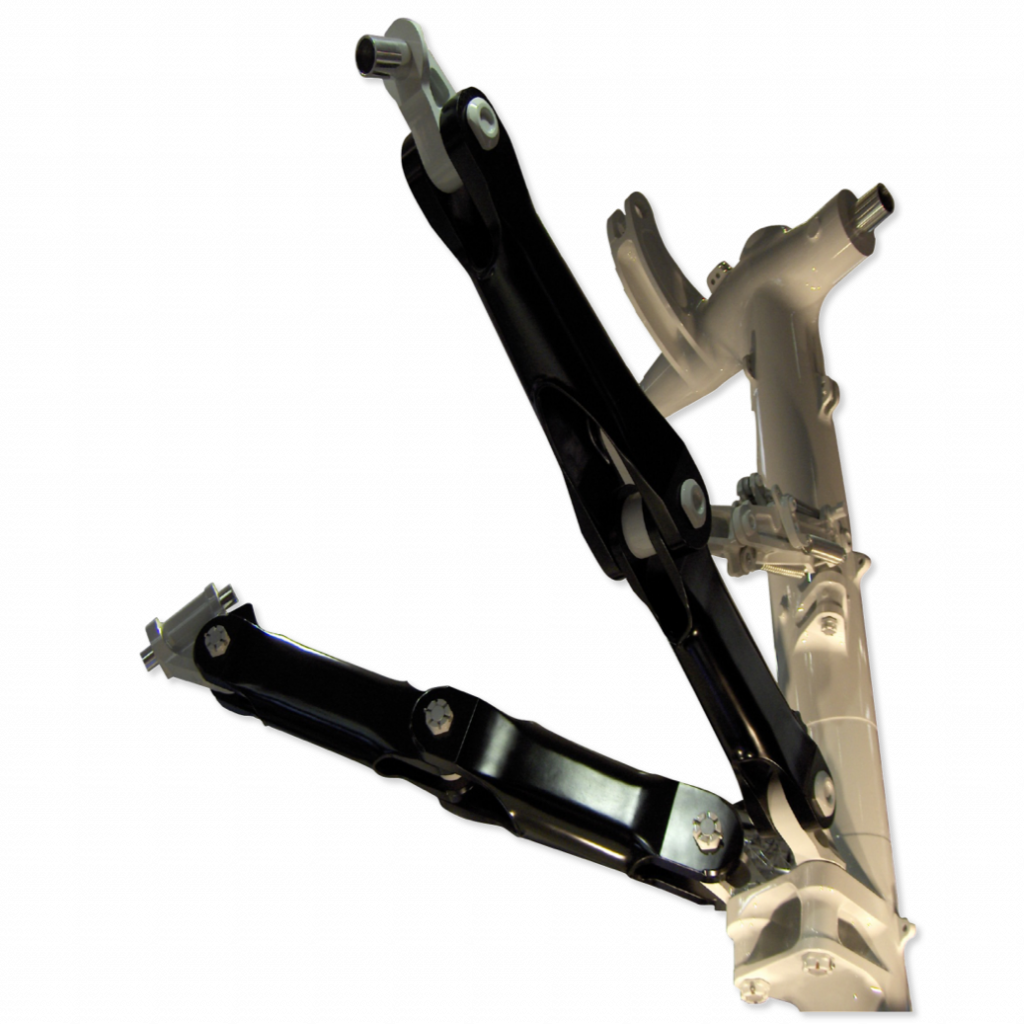
Composite fabrication processes involve some form of molding, to shape and consolidate the resin and fiber reinforcement. A mold is required to give the unformed resin/fiber combination its shape prior to and during cure. Our group has had extensive experience in various molding technologies and we even developed new and innovative processes for greater efficiency and performance. We have a proven expertise in the following technologies and processes:
- Resin Transfer Molding (RTM and VaRTM)
- Infusion
- Thermoplastic
- Prepreg
- FPTM : Final Pressure Transfer Molding
- Bonding/adhesive applications
- 3D or 2D conventional or complex preforms

Our experts can help you to define the best manufacturing technology, processes and tooling adapted to your needs.